In Line Boring
INTRO
Line Boring
Construction Equipment Line Boring
Construction equipment is among the most common hydraulic equipment to require line boring repairs. Such heavy machinery often experiences high levels of stress on bored joints that can cause them to fail. The fact that much of this equipment is often left out in the elements does not help. Once the outer coating of paint has been chipped, rust can form around key load-bearing points.
Bore welding and line boring can be used to repair breaks and enlarge and realign existing, damaged boreholes. For heavy equipment, on-site line boring is an economical repair option because it means you do not have to bring that equipment to a repair shop. On-site repairs for such equipment is often quicker, resulting in less downtime and lost revenue.

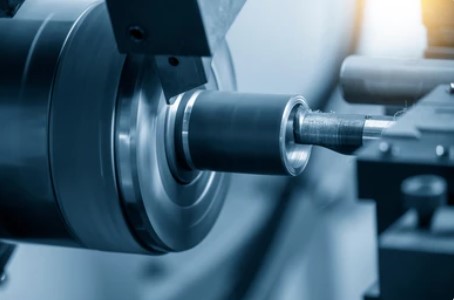
Hydraulic Machinery Line Boring & Repair
At WAPS Global, we make use of SPR York portable line boring machines to repair your equipment on-site. This tool can bore holes with diameters from 3” – 24”. It also has up to 351 ft. lbs. of torque at the bar, allowing it to cut through heavy materials easily. By using portable tools such as this, we can often avoid major disassembly of your heavy equipment, making the repairs even faster and less costly.
Bore welding, also called weld cladding
A worn bore can be reworked to original size by bushing, but if there is insuffient material to maintain the grip through interferance fitting, the bush may work loose with detremental effect. A solution to this problem is to weld clad the bore so it is under size and then line bore to finished size. This process ensures that there is no risk of anything fretting or working loose. Our bore welding machine is fully mobile and can work in any position. It can weld bores from 40mm to 700mm. Each pass of weld will lay upto 5mm of metal once machined smooth, thus reducing the bore by upto 10mm on every pass. Succesive passes can be made on top of existing passes. Our fully portable machine can work in conjunction with our line boring equipment at your site and generators can be provided to sites with insufficient power supplies.
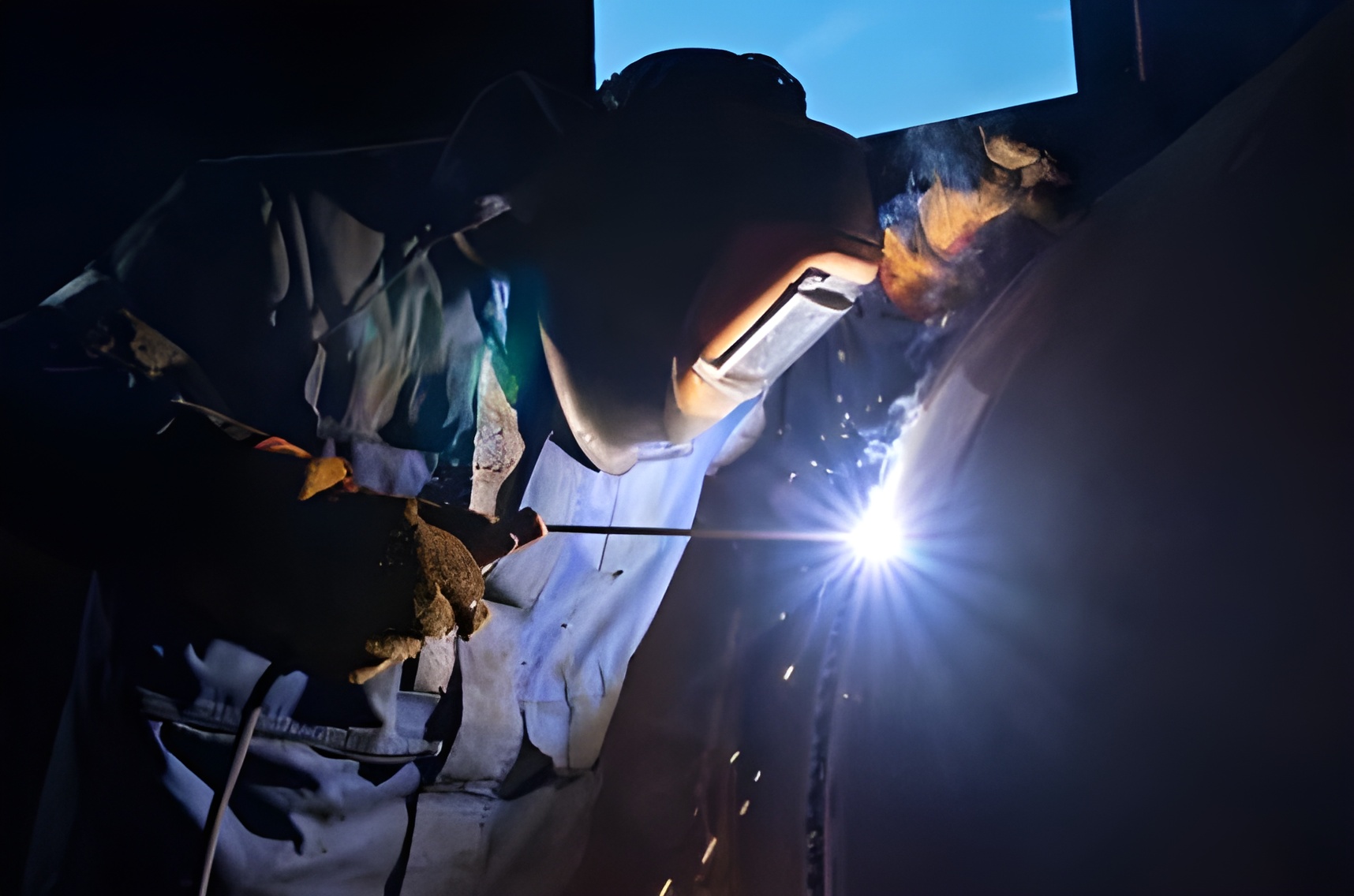
Bore Welding
Bore Welding is a welding process that reduces the diameter of a bore by adding 3-6mm of metal to the inside of a worn bore which can then be machined back to the correct size with the line boring process. Usually a pre-machining process is carried out, ideally 1-2mm deep to provide a clean metal surface for the welding process. The correct welding procedure should be used for each individual application. One option is to pad weld by hand the area that needs to be repaired. However, using the bore welding machine will result in a much more consistent weld with less chance of slag inclusion and imperfections. We can weld bores from as little as 40mm diameter and out past 500mm diameter.
Dry Ice Cleaning
The Benefits
We save you precious time. Some of these repairs can be carried out in as little as 24 hours
- We save your money. The equipment does not have to be stripped down and transported or re-assembled. The savings on this alone are usually very significant
- We keep your plant running. Downtime is minimized so that you can be back in production and earning a return much sooner.
Other Services We Do:
To help to get the vessel as quick as possible out of the dock, we can normally work 24/4 with short notice.
Services
- Line Boring
- In Situ Milling
- Internal Diameter Welding
- Face Welding & Repairs
- Face Machining
- Flange Facing
- Broken Tap/Stud Removal
- Acoustic Alignment
- Spark Erosion
- Bush & Bearing Installation Capabilities
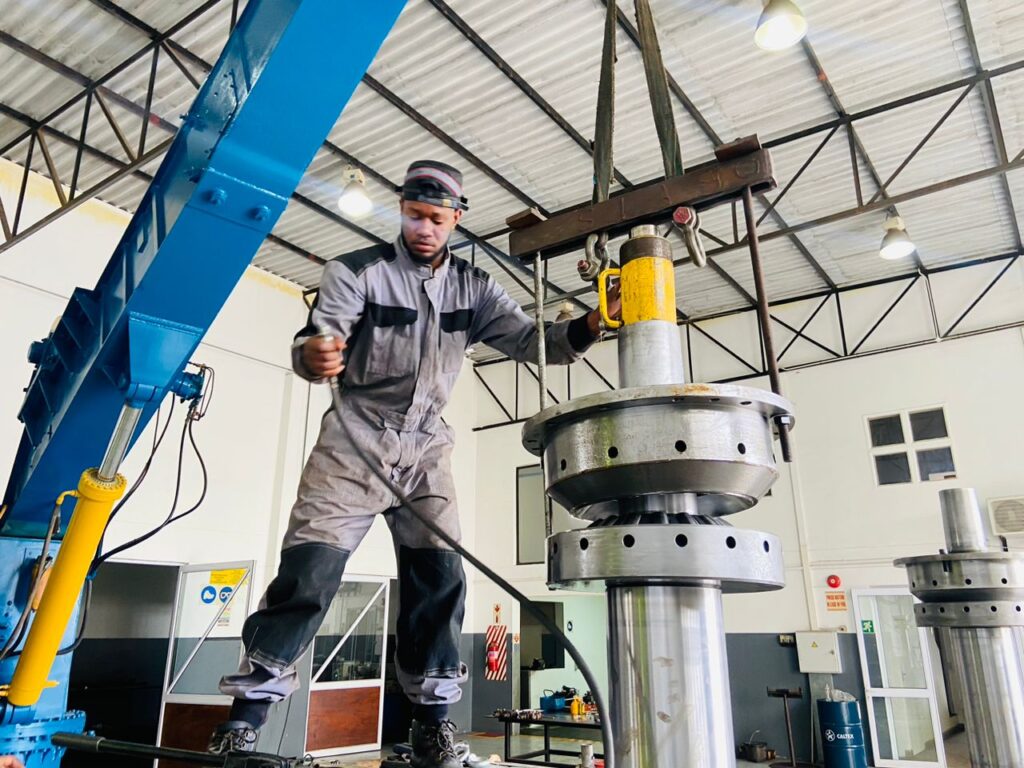
On-Site & In-Situ Line Boring
Nicol & Andrew have been line boring main bearing pockets, turbine casings, tail shaft bores, rudder bores and industrial equipment bearing housings for decades. With our latest Laser guided boring equipment, we can now correct even the slightest misalignment problem on every size and range of diesel engines or marine/industrial plant.
Our new flexible setup fixtures can cope with lengths up to 12 meters and diameters over a metre. We can machine main bearing pockets and caps on any engine. We can also carry out on-site line boring to engine blocks, propeller housings and ships steering gear.
In situ line boring, also called line boring, in situ boring, shaft boring.
Worn bores for bearings, pins and bushes etc can be machined and refurbished at your site or in our works to the original manufactured size by bushing or weld cladding (see bore welding below). Our fully portable line boring machines can accomodate bores from 30mm to 700mm in diamater and can be set up ready to machine in an hour. Perfect alignment can be achieved by the adjustable bearing blocks and H7 tolerances are easily met. The fully portable machine can machine cast iron, carbon steel, stainless steel and bronzes/white metal. The advantages of in situ machining are that there is reduced equipment down time, less removal time and zero transport costs. We can also offer an on site pressing service to install new bearings, pins and bushes if needed.